Precision Plastic Injection Molding: Revolutionizing Manufacturing
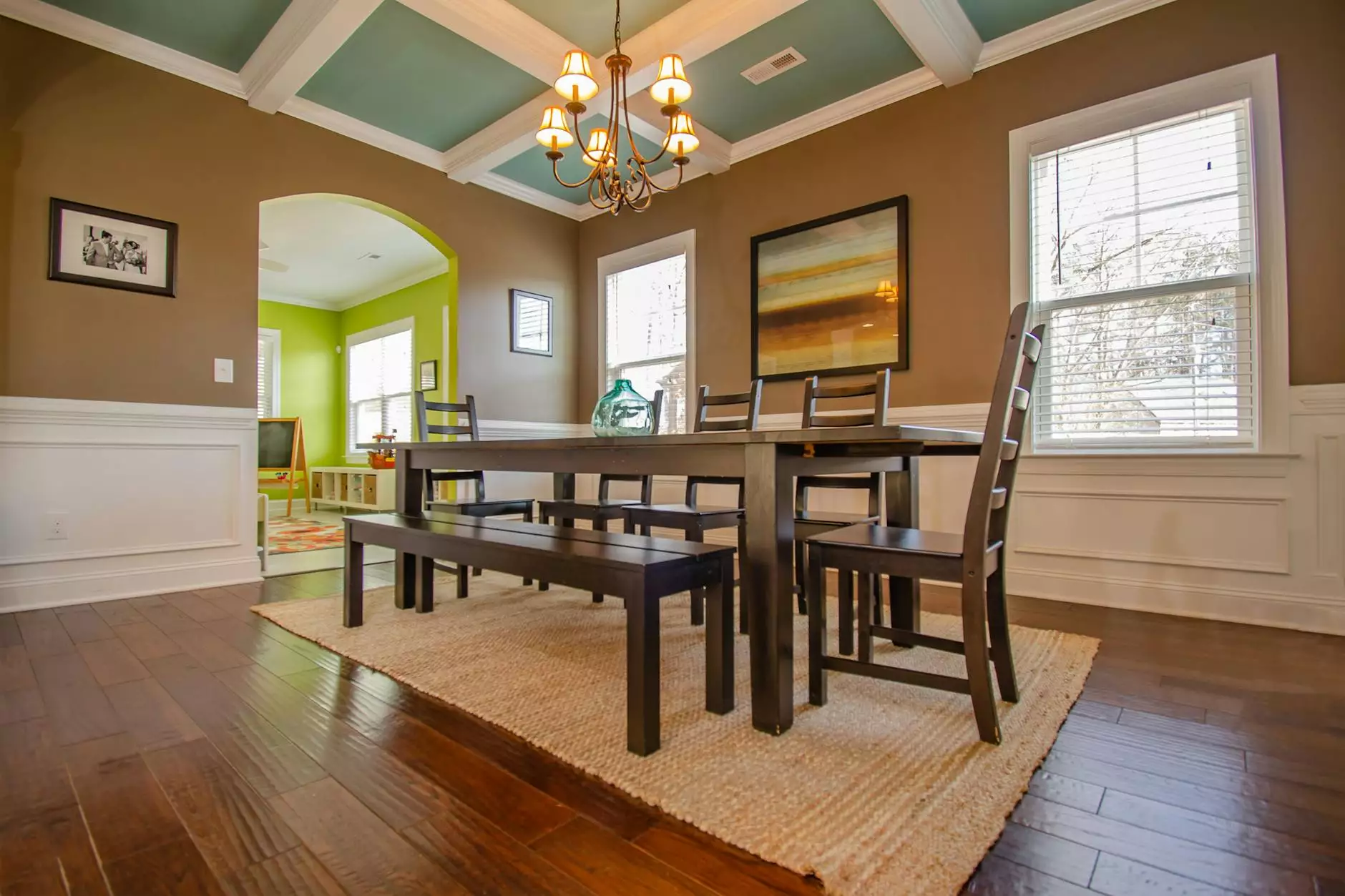
The quick evolution of manufacturing technology has paved the way for innovative solutions that increase efficiency and reduce costs. One such revolutionary technique is precision plastic injection molding, a crucial process utilized in the production of high-quality plastic parts. This article aims to provide an in-depth understanding of this technique, its applications, advantages, and its significant role in the realm of metal fabrication.
Understanding Precision Plastic Injection Molding
At its core, precision plastic injection molding is a manufacturing process that involves injecting molten plastic into a mold to form a specific shape. The precision aspect refers to the ability to produce remarkably accurate parts within tight tolerances. This capability is essential for various industries, including automotive, aerospace, consumer goods, and medical devices.
The Process of Injection Molding
The precision injection molding process can be broken down into several key stages:
- Material Selection: The process begins with selecting the right plastic material for the job, often thermoplastics that can withstand high temperatures.
- Mold Design: A precision mold is designed using computer-aided design (CAD) software, ensuring that it meets the exact specifications needed for the intended application.
- Heating: The selected plastic is heated until it becomes molten, allowing it to flow easily into the mold.
- Injection: The molten plastic is injected into the mold at high pressure, ensuring that it fills every detail of the cavity.
- Cooling: The mold is cooled, solidifying the plastic into a finished part. This step is crucial for maintaining dimensional accuracy.
- Finishing: The part is ejected from the mold, and any necessary finishing touches are made, such as trimming or polishing.
Why Choose Precision Plastic Injection Molding?
There are numerous reasons to opt for precision plastic injection molding over other manufacturing methods:
1. High Precision and Accuracy
One of the most significant advantages is the process's ability to produce parts that adhere to strict tolerances. This precision is vital for applications requiring exact specifications, where even minor deviations can lead to catastrophic failures.
2. Efficiency and Scalability
Once the molds are created, production can be scaled rapidly, allowing manufacturers to produce large quantities of identical items in a short timeframe. This efficiency leads to lower production costs per unit, making it economically viable for a variety of projects.
3. Versatility in Material Use
Precision plastic injection molding supports a wide range of plastic materials. From rigid polymers to flexible elastomers, this molding technique can accommodate various material properties tailored to specific applications.
4. Reduced Waste
With the precision design of molds and the efficiency of the injection process, material waste is significantly reduced compared to other manufacturing methods. This not only lowers costs but also aligns with sustainability practices by optimizing resource use.
5. Enhanced Design Complexity
Injection molding allows for intricate designs and fine details, making it feasible to create complex geometries that would be impossible with traditional manufacturing techniques.
Applications of Precision Plastic Injection Molding
The versatility of precision plastic injection molding has led to its widespread adoption across several industries:
1. Automotive Industry
In the automotive sector, precision-molded components are essential for making parts like dashboards, interior trim, and even engine components. The use of lightweight plastics improves fuel efficiency without compromising safety and performance.
2. Medical Devices
The medical industry relies heavily on precision molding for the production of medical devices, such as syringes, inhalers, and surgical instruments. Here, strict adherence to safety and cleanliness standards is paramount, making precision molding technology indispensable.
3. Electronics
Precision injection molding is crucial for manufacturing enclosures and components for electronic devices. The need for finely detailed and dimensionally accurate parts, along with the ability to incorporate multiple materials, makes this technique ideal for electronic applications.
4. Consumer Goods
Household items, toys, and appliances benefit from the efficiency and design flexibility offered by precision plastic injection molding, allowing companies to deliver quality products to market rapidly.
Challenges in Precision Plastic Injection Molding
While precision plastic injection molding offers numerous advantages, a few challenges can arise:
1. High Initial Setup Costs
The cost of designing and manufacturing molds can be significant, making precision plastic injection molding more suitable for high-volume production runs.
2. Complexity in Process Control
Maintaining the precision of the molding process requires careful control over various parameters, such as temperature, pressure, and cooling time. Even minor variations can lead to defects.
3. Limitations in Material Properties
Different plastics have unique properties, and not all can be efficiently processed through injection molding. Understanding the material's characteristics is key to successful production.
Future Trends in Precision Plastic Injection Molding
The future of precision plastic injection molding appears promising, with ongoing advancements in technology that are set to transform manufacturing:
1. Smart Manufacturing
Integrating IoT (Internet of Things) technologies can enhance monitoring and control processes, resulting in increased efficiency and predictive maintenance of machinery.
2. Sustainable Materials
With a growing focus on sustainability, there is an increasing interest in biodegradable and recycled materials for injection molding, pushing the boundaries of eco-friendly manufacturing.
3. Advanced Simulations
With the rise of AI and deep learning, simulation tools are becoming more sophisticated, allowing manufacturers to predict outcomes and optimize the injection molding process before actual production.
4. 3D Printing Integration
The ability to integrate 3D printing with conventional molding processes can enhance design flexibility and reduce lead times during prototyping stages, blurring the lines between rapid prototyping and mass production.
Conclusion
In summary, precision plastic injection molding represents a transformative approach to manufacturing, offering unparalleled precision, efficiency, and versatility. As industries continue to evolve, embracing this innovative technology is vital for staying competitive. Companies seeking to leverage the benefits of precision molding should consider partnering with experienced fabricators capable of harnessing the full potential of this remarkable manufacturing process.
At DeepMould, we specialize in delivering high-quality precision plastic injection molding services that meet the diverse needs of our clients across various sectors. Together, we can drive innovation and excellence in manufacturing.